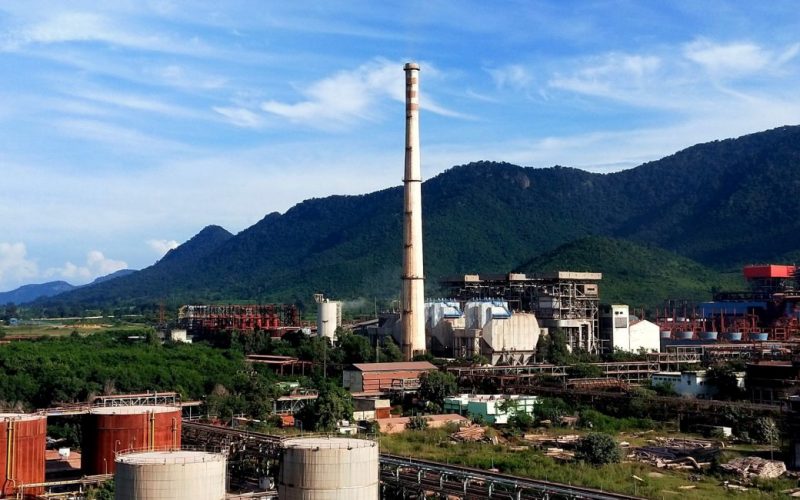
IIT Kharagpur develops cutting-edge technology to reduce Red Mud by Alumina refining
IIT Kharagpur and Vedanta Aluminium have developed a process to significantly reduce the generation of bauxite residue, commonly known as red mud, in the alumina refining process. The patented process reduces bauxite residue by a remarkable 30 per cent by eliminating iron values while simultaneously recovering a higher alumina yield, reducing the total organic content of bauxite during the alumina refining. The process significantly enhances resource efficiency and curbs energy consumption during refining. The project was led by the Research and Development Department of Vedanta, the country’s leading aluminium producer, in collaboration with the Department of Metallurgical and Materials Engineering,…