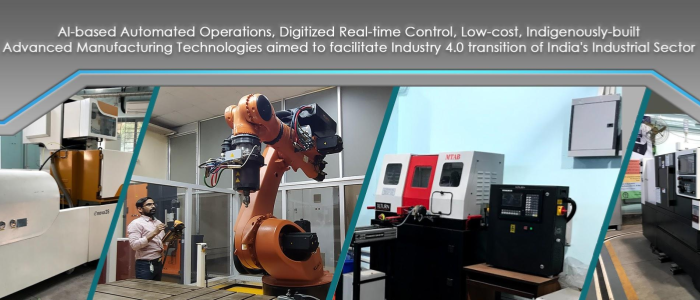
Industry 4.0 to create new job opportunities through digitization of industrial operations
By Prof. Surjya K Pal Overview of Industry 4.0 The fourth industrial revolution, popularly referred to as Industry 4.0 constitutes a plethora of technological concepts aiming towards the adoption of cyber-physical systems. Essentially, it involves connecting the segments of a manufacturing system with digital technologies for gaining critical and real-time insights. The technologies include the use of intelligent robots, real-time monitoring and control of manufacturing systems, cloud, edge, and fog computing, all of which will lead to the development of the Industrial Internet of Things. At present, Industry 4.0 is at a very nascent stage, and a large number of…