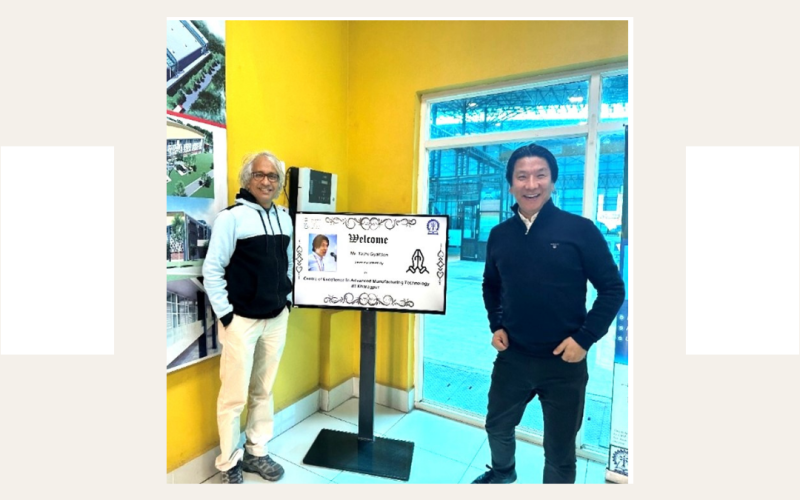
Strengthening Global Research Ties with Swansea University, UK
IIT Kharagpur Forge Strategic Partnership with Swansea University in Advance Smart Manufacturing and Materials Research In a significant step towards global academic and industrial collaboration, Swansea University and the Indian Institute of Technology Kharagpur (IIT KGP) signed a Memorandum of Understanding (MoU) to deepen research partnerships, promote academic exchange, and foster innovation in advanced manufacturing and materials engineering. The collaboration was strengthened by a visit from Mr. Tashi Gyaltsen, a representative of Swansea University to IIT Kharagpur’s Centre of Excellence in Advanced Manufacturing Technology (CoEAMT) on 27 January 2025. This visit, recommended by their collaborator Tata Steel UK, aimed to…